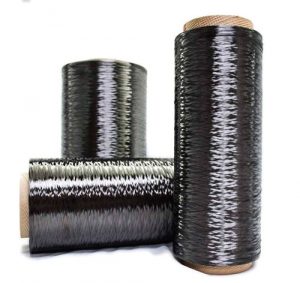
Textiles are the unsung heroes of our everyday lives
TWSpecial Report
Textiles are the unsung heroes of our everyday lives. Innovative problem-solvers — experts tackling some of the world’s biggest challenges to provide comfort, convenience, protection and utility — personify the industry. From aircraft engines to automotive fabrics and athletic wear, American textile industry ingenuity is improving the performance of a wide array of products.
Lighter Engines
当你想到纤维,你可能我nitially think of natural options like wool or cotton. You might also think of man-made fibers like polyester or nylon. But what about carbon fiber? Carbon fiber is tightly woven throughout our daily lives but often goes unnoticed except to trained eyes.
Stamford, Conn.-based Hexcel Corp. is a leading carbon fiber manufacturer. Beginning with its polyacrylonitrile (PAN) precursor production site in Alabama, Hexcel manufactures carbon fiber with a focus on composite materials that reinforce plastics to help build structures.
“Hexcel is continuing to develop fiber and technology in product forms that meet the needs of those wanting to go faster, stronger and lighter,” said Tom Haulik, sales director of carbon fibers.
Rockets, airplanes and Formula One race cars are just some of the high-tech structures supported by Hexcel’s miraculous fiber. Carbon fibers can either be woven into broad goods and then used to reinforce plastics, like in a car panel, or braided and compressed into a tube to form objects like hockey sticks and golf club shafts.
Another amazing application involves the aircraft industry. While most air passengers would assume their seats are made from textiles, they may not realize an engine made from textile parts is propelling them to their destination, thousands of feet in the air. Aircraft engine components using carbon fiber are woven into 3-D structures and then infused with resin. These high-strength carbon fibers create a remarkably lightweight, durable and reliable engine that is also fuel-efficient.
Safer Landings
常旅客依靠一个强大的引擎off but need reliable brake discs to make a safe landing. For example, the carbon brake pads that bring your plane to a stop on the runway are created with Pyromex®, a textile from Toho Tenax manufactured in Tennessee. Instead of a metal-based disc, these highly efficient and durable brakes start as a carbon fiber-based felt fabric, which the manufacturing process transforms into a black, brick-shaped brake for aircrafts.
This incredible textile is produced without additional Bromine/haline compounds, making Pyromex® ideal to meet regulatory requirements for flame resistance on one hand and environmental health on the other. The Limiting Oxygen Index (LOI) of Pyromex also is much higher than other organic flame-resistant fibers, making it a durable alternative. Pyromex is widely used in welding blankets, fleece insulation and carbon brake applications to help keep passengers safe.
Smarter Apparel
In today’s world, phones double as a personal assistant, personal trainer, grocery list and talking watch. Convenience is king, and smart products are becoming more deeply immersed in our culture and everyday lives. Groundbreaking smart textiles are no exception.
We intuitively know apparel serves many purposes: It shields us from the elements and serves as a form of personal expression. But some clothing is engineered to deliver even more user benefits.
Pulcra Chemicals, a Rock Hill, S.C.-based global manufacturer of specialty chemicals for fiber, textiles and leather, makes sure clothes do more than simply provide function or fashion. The company’s Skintex® technology embeds microcapsules filled with high-grade ingredients into fabric during the chemical finishing stage of production. The contents of those microcapsules then are slowly released onto the wearer’s skin.
For example, yoga pants are popular activewear. Yoga pants made with Skintex micro-encapsulated, high-grade lotions and vitamins applied to the fabric provide moisturizing effects throughout the day. Looking forward to a relaxing evening? Pajama pants enhanced with Skintex release a micro-encapsulated aromatherapy with the light scent of lavender to create a calming effect before the start of a hectic week.
Besides making consumer products more luxurious, Pulcra’s Skintex line is also having a humanitarian impact.
Skintex业务经理Troy Massey说:“ Skintex MRIII毯子是一种特殊的,无编织的织物,我们用驱虫剂处理。”“这不是您典型的舒适毯子,而是在户外使用的产品。猎人经常将其用作地面盖。随着最近在撒哈拉以南非洲进行的寨卡病毒爆发和正在进行的疟疾之战,我们使用环境保护局注册的Skintex MRIIII毯子产生了影响。我们向坦桑尼亚的小学生捐赠了11,000个毯子,以帮助与疟疾作斗争。我们还与一些美国奥林匹克运动员一起向里约热内卢派遣了Skintex MRIII毯子,包括游泳,跆拳道和水球球队。我们正在继续努力为这次爆发提供帮助,因为这仍然是一个大问题。”
More Versatile, Sustainable Finishes
Schoolchildren learn about three states of matter: solid, liquid and gas. But what about the fourth state of matter, plasma?
If energy is applied to a gas, it becomes ionized and goes into an energy-rich plasma state. Plasma is all around us; for example, polar lights in the Arctic and Antarctic skies show plasma in its natural form.
APJeT, a Morrisville, N.C.-based textile technology company, is using plasma to revolutionize the way fabrics are finished, the point in production when chemicals are applied to improve a fabric’s look, performance and feel.
Called the “wet process” because of its water-based nature, the worldwide textile industry uses trillions of gallons of water to finish fabrics each year. Water scarcity and quality degradation are major global concerns, but APJeT’s plasma technology is eliminating the need for water in the fabric finishing process. Compared to the wet process, the company’s sustainable plasma solution also significantly reduces chemical consumption.
Innovators at APJeT are harnessing the power of plasma to create engineered solutions for a variety of applications:
- protective fabrics for military ballistics and defense;
- outdoor soil- and water-repellent fabrics;
- nonwoven fabrics used in diapers and disposable medical garments;
- automotive fabrics that reduce staining and soiling; and
- film membranes that create scratch-resistant surfaces and protective coatings for electronics.
“Our process is a complete paradigm shift in how textiles are produced and finished,” said President and CEO John Emrich. “Our post-finishing process solution eliminates the need for water, ovens and high energy. This technology allows APJeT to apply durable, performance-enhancing finishes to anything including films, silks, polyesters, cotton and polypropylene, and it’s changing the way we think about the finishing process in our industry.”
Today, American textiles are transforming countless products from massive aircrafts to needle-thin fibers to create smarter, more durable solutions. By devoting itself to the relentless hunt for engineered solutions and seamless processes, the U.S. textile industry is solving problems worldwide.
Editor’s Note: This article appears in188BET金博宝下载courtesy of the National Council of Textile Organizations (NCTO) as part of the “American Textiles: We Make Amazing™” campaign. NCTO is a trade association representing U.S. textile manufacturing. Please visit ncto.org to learn more about NCTO, the industry and the campaign.
May/June 2017