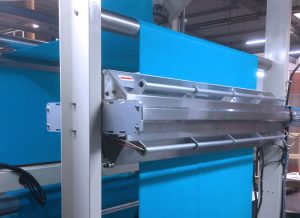
STOCKHOLM, Sweden — October 25, 2021 — Members of TMAS — the Swedish textile machinery association — are proving instrumental in pioneering new sustainable processes for the dyeing, finishing and decoration of textiles.
浪费在这些基本过程ring stages are only one component in the development of viable circular supply chains for textiles that are now being aggressively established in Sweden.
在9月30日,10月1日和10月7日在三个单独的下午举行的纺织品可持续饰面会议上,代表们听说瑞典将在2022年初开始对废物纺织品和服装引入扩展的生产者责任(EPR)2025年采用了类似的欧盟范围内EPR系统。
在瑞典,这已经导致建立先进的数字排序和回收基础设施,从品牌的角度来看,H&M现在领导着该领域,这两者都从供应商中探讨了循环系统,并最大程度地减少了自己的废物。
New fibers
Swedish companies are also active in the development of new fibers derived from waste clothing, building on the country’s legacy leadership in pulp and paper production.
At the Sustainable Finishing of Textiles Conference, however, it was said that all of the environmental gains made by such sustainable new fibers can potentially be cancelled out in the further processing they are subjected to — and especially in resource-intensive conventional dyeing, finishing and decoration.
TMAS成员Baldwin Technology和Coloreel都开发了解决此问题的解决方案。
TexCoat G4
During the conference, Baldwin’s VP of Global Business Development Rick Stanford explained that his company’s TexCoat G4 non-contact spray technology significantly reduces water, chemistry and energy consumption in the finishing process. It consistently and uniformly sprays chemistry across a fabric surface and applies it only where needed, on one or both sides.
“Customers can expect no bath contamination during the finishing process, as well as minimal downtime during changeovers, which are made easy with recipe management that includes automated chemistry and coverage selection,” he said.
The TexCoat G4 also wastes no chemistry during color, fabric or chemistry changeovers, and because only the required chemistry volume is applied to the fabric, wet pick-up levels can be reduced by up to 50 percent — leading to 50-percent less water and energy consumption compared to conventional finishing processes. Furthermore, several customers are combining TexCoat Spray and back-coating in series prior to the stenter. This simplifies the production process from two steps to one, delivering both drying savings and productivity increases.
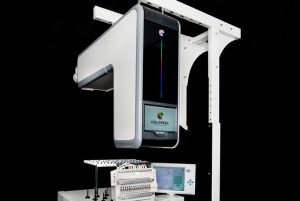
即时着色
Coloreel’s CEO Mattias Nordin outlined the benefits of his company’s technology which enables the high-quality and instant coloring of a textile thread on-demand and can be paired with any existing embroidery machine without modification. This enables unique effects like shades and gradient to be achieved in an embroidery for the first time.
Nordin说:“我们的技术现在已经商业化,我们正在广泛地扩大业务。”“公司的基础是基于这样的想法:那里有数百万种螺纹卷轴,其中许多将变得过时并变成浪费,并且在使用该线程时染色将更简单。这就是我们所取得的成就。”
Based on a CMYK ink system, Coloreel’s advanced rapid coloring software and high-speed drive technology allow a single needle to carry out what previously required multiples of them to do – and with much more consistent stitch quality,
In addition, existing thread dyeing plants can add a single solid color to a thread, but by instantly coloring a white base thread during production, Coloreel enables complete freedom to create unique embroideries without any limitations in the use of colors. Color changes along the thread can either be made rapidly from one solid color to another, or gradually, to make smooth transitions or any coloring effect desired.
这在可持续性方面提供了巨大的好处。浪费的油墨量显着降低,而用水量则最小化,生产速度增加。该技术允许减少设置和交货时间,以及生产量的显着灵活性,同时消除了对大型线程库存的需求。
Nordin说:“我们的系统允许客户实现从未有过的颜色效果,并且以新的效率水平。”
“It’s great to see TMAS members playing a pioneering part in what is now shaping up to be a vital rethinking of the textile supply chain here in Scandinavia,” added TMAS Secretary General Therese Premler-Andersson. “All of these ideas are now gaining momentum and likely to be adopted throughout the world. A more circular and sustainable industry will be the result, to the benefit of everyone.”
Posted October 25, 2021
资料来源:TMA-瑞典纺织机械协会